Understanding the difference between “hydrophilic” and “hydrophobic” is a big deal when it comes to anti-fog safety glasses.
Most workers in the industrial space are aware of the need for anti-fog lens coatings, but what they probably don’t know is the science behind these two kinds of anti-fog technologies and how they work.
Simply put, ‘hydrophobic’ means water adverse, and ‘hydrophilic’ means water-loving.
Hydro – water
Phobic – having a fear or aversion to a specific thing
Philic – having a fondness, especially an abnormal love, for a specified thing
Now, let’s break down the differences.
Hydrophobic
Most coatings in the Australia and New Zealand market are hydrophobic.
A hydrophobic coating is soap-based and works by repelling moisture, spreading the droplets across the lens. This ultimately leads to a buildup of fog on the lens, which requires cleaning to remove it. Eventually, depending on the quality of the coating, the detergent properties will be washed from the lens, rendering it ineffective.
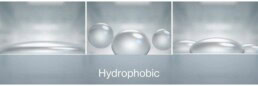
While this is effective for a short period of time, environments with heavy fogging will end up causing severe visibility issues as the moisture builds up on the lens, compromising compliance.
What’s more, this kind of coating will wash off over time due to its soap-based qualities.
Hydrophilic coatings
Moisture-loving coatings are known as hydrophilic.
Unlike hydrophobic coatings that repel water, hydrophilic coatings act like a microscopic sponge by interacting and absorbing moisture into the coating –eliminating fogging almost instantly.
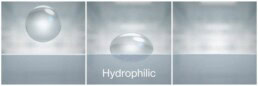
The coating is able to hold a high amount of moisture and naturally releases that moisture at the edge of lenses, making hydrophilic lenses difficult to fog up.
Additionally, hydrophilic coatings are not soap-based, meaning they won’t wash off like hydrophobic coatings. That’s because hydrophilic coatings are made with a proprietary chemistry that creates a polymer bond, permanently adhering the coating to the polycarbonate lens.
When do you need an anti-fog coating?
Understanding the environment you work in should have a significant impact on the lens coating option you select on your safety eyewear. Anti-fog coatings on safety glasses are especially important in environments where temperature and humidity changes are frequent or where you’re exerting yourself physically. Some examples include:
- Industrial and construction sites – High humidity environments
- Cold storage and food processing – Constant movement between different climate zones.
- Medical and laboratory settings – With frequent us of other PPE like face masks.
Environment is just one of the selection criteria when choosing the right safety eyewear for you. Here are four things to consider before purchasing safety eyewear.
uvex coating expertise
uvex anti-fog coatings are advanced lens treatments designed to provide long-lasting clarity in challenging environments. Coatings, such as our supravision THS deliver superior fog resistance, making them ideal for high-humidity, high-exertion, or rapid temperature-change conditions. Unlike standard anti-fog solutions, uvex coatings are permanently bonded to the lens for extended durability and performance, ensuring users maintain a clear view while staying safe and focused on the task. Perfect for industrial, medical, and outdoor applications.
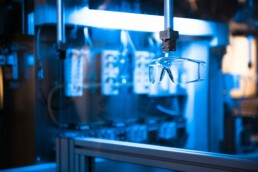
uvex supravision THS
Lenses coated with uvex supravision have advanced anti-fog performance on both sides. The anti-fogging properties are permanent, even after being repeatedly cleaned.
Explore the range
Need help finding the right eye protection?
Unsure about which product right for your application or environment? Reach out to one of our uvex Safety Solution Specialist.