Electrostatic build-up and its uncontrolled discharge can have serious consequences for people – we examined this in detail in a previous article. Now we intend to discover what actually makes PPE capable of discharging electrostatic build-up, how it can be checked and what products uvex offers in this areaet.
In the past, the majority of protective clothing used in the field of ESD was 100% cotton. As with all natural fibres, this offers the advantage of being subject to only minimal antistatic build-up without the use of additional equipment. However, humidity plays a key role here: the natural material is in itself hygroscopic – i.e. it draws in moisture from the air, thereby increasing its static dissipative capacity in high-humidity environments. However, if the air is rather dry, cotton clothing lacks the requisite fibre moisture; it loses its natural discharge capability and this can lead to dangerous build-ups. Cotton also poses a hazard in that its staple fibres can come loose. On account of opposing charges, these fibres then cling to the components which also causes issues. Using long, high-quality staple fibres counteracts this problem.
Fibres for antistatic and/or ESD applications
Chemical fibres such as polyester are, in contrast, continuous fibres. This significantly reduces the risk of contamination through loose fibres. One disadvantage, however, is that this can be subject to quite substantial friction build-up, as in contrast to cotton it is not hygroscopic. In order to limit these build-ups and conform with the antistatic and ESD standards alike, the garment must also include additional fibres or threads. Threads and fibres such as the conductive Resistat® (synthetic core with a carbon coating) and the static dissipative Nega-Stat® (polyester-coated carbon core) are used for this. Using these fibres and threads is now standard practice and they can be found in blended fabrics and textiles made from 100% cotton.
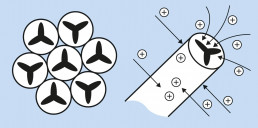
1) Systematic representation of a Nega-Stat®fibre
The use of carbon minimises resistance and therefore facilitates the controlled discharge of build-up. For ESD applications, the static dissipative/conductive fibres must be on the outer layer due to defined test procedures. For example, Resistat® is therefore used for our ESD shirts. Moreover, the fibres for woven products must be arranged in a mesh pattern (maximum area of 5 x 5 mm² per square) in order to ensure the necessary charge decay. For knitted fabrics, the fibres must correspondingly be integrated into the stitch formation. In addition, static dissipative/conductive fibres are used for the closing seams.
Use of static dissipative/conductive fibres for ESD applications
However, for antistatic applications, whether the core or coating of the product is conductive or static dissipative is not important. In order to fulfil the antistatic standard EN 1149-3 (charge decay), a mesh pattern (smaller than 10 x 10 mm²) or threads arranged in parallel (at a distance of less than 10cm) must also be integrated on the exterior surface.
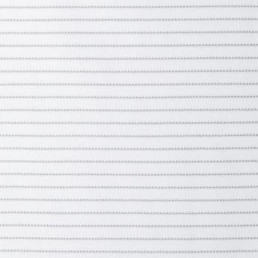
Knitted fabrics (ESD)
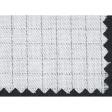
Woven fabrics (ESD)
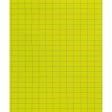
Mesh pattern with carbon fibres
Are there any other requirements?
In choosing conductive or static dissipative additional components, the area of application must be taken into consideration. For instance, for ESD work it is very important to ensure that optimal skin compatibility is offered, as ESD t-shirts, for example, are in direct contact with the skin.
It is only in exceptional cases that protection in compliance with EN 1149 is the only requirement to which clothing is subject: for example, antistatic protection is often required for chemical PPE – after all, when dealing with chemicals, environments which feature sensitive air-gas mixtures are a common occurrence. Other areas of application include wood processing and metalwork: when welding in dusty environments, employees’ PPE must comply with the antistatic standard in addition to standards regulating heat and flame protection as well as welding protection.
ESD = antistatic? A glance at the test criteria
It is often asked whether ESD clothing can be used for antistatic applications and vice versa. Unfortunately, a comparison with regard to the antistatic properties of ESD clothing and antistatic clothing is not as clear cut as it is with safety footwear, for example. With safety footwear, the contact resistance defined in the standard applies. Here, the values can be easily and clearly compared with one another. A comparison of this sort for the test requirements is unfortunately not possible for this type of protective clothing. Within the framework of the antistatic standard, there are three testing criteria depending on the material used and potential equipment. Only one of these has to be fulfilled in order to receive certification.
- EN 1149-1 surface resistance < 2.5 x 109 Ω
- EN 1149-2 contact resistance
- EN 1149-3 50% charge decay in less than 4 seconds or shielding factor S > 0.2
EN 1149-5 provides additional information on the respective test parameters pertaining to EN 1149-1, EN 1149-2 and EN 1149-3.
In contrast, the ESD standard applies two test criteria which both have to be met:
- Point-to-point resistance (< 1011Ω)
- Charge decay (from 1,000 V to 100 V in less than 2 seconds)
ANTISTATIC (EN 1149-1; EN 1149-2; EN 1149-3; EN 1149-5)
ESD EN 61340-5-1 (EN 61340-5-2)
Material
Base material with special fibres or threads (to increase static dissipative properties)
synthetic fibre with hygroscopic properties (drawing moisture from the air)
Polyester blend fabric with additional special fibres or threads (e.g. carbon for improved electrostatic conductivity)
Conductive fibres
Conductive coating or core
Conductive coating (always used)
Before testing
5x wash cycles
Mint condition
Testing
One of three testing procedures:
- 1149-1 Surface resistance (a) fibres with conductive coating b) surface material with corresponding equipment e.g. for disposable protective clothing in use) < 2.5 x 10 9 Ω
- 1149-2 contact resistance
- 1149-3 charge decay (with conductive surface core or coating) 50% < 4 seconds or shield factor S > 0.2
Point-to-point resistance (<1011Ω)
and
charge decay (from 1,000 V to 100 V (10%) in < 2 seconds)
Performance requirements:
1149-5 testing parameters for 1, 2 and 3
In accordance with the standard, only a single material test must be conducted (uvex always tests the entire garment system in collaboration with the Sächsisches Textilforschungsinstitut Stfi [Textile research institute of Saxony] for the purposes of safety)
The entire garment is subjected to testing
What the two standards do have in common is testing charge decay; however, the requirements for the ESD standard are significantly higher than for the antistatic standard. The testing conditions are also very different. Within the framework of the antistatic standard, only the surface material must currently be tested. For ESD certification, however, the entire garment must be tested and assessed. As we believe that testing the entire garment has many advantages, uvex PPE is always tested in this way. This means that seams and other transition points, which often present weak points in clothing, are also taken into consideration.
After outlining the fundamental differences in the protection level offered by both standards in the first article – and learned that the antistatic standard centres on PPE to protect humans, while the ESD standard deals with protecting objects against very weak build-ups – we went into more detail in this second article. Generally speaking, a mesh pattern/lined fabric structure can be regarded as the first indication that conductive/static dissipative fibres have been used. Taking a quick glance inside the garment allows the relevant standard on the label to be quickly tested. In addition, nearly every PPE product made by uvex comes with a relevant pictogram on the exterior.
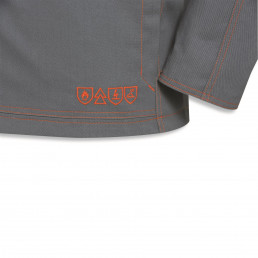
Example for pictograms at the uvex heat shell
As well as dealing with the material, we have compared and explained the testing criteria for both standards. These criteria seem similar at first glance, but in actual fact a direct comparison is not feasible. The working environment and corresponding activity must be taken into consideration when choosing the correct PPE – this stays true to our philosophy of: “protecting people“.
Good initiative for better future
Great post, thanks