The terms ESD and anti-static are often used interchangeably in the context of occupational health and safety. In this blog article, we answer the question “what is ESD?”, explain the difference between anti-static and ESD, and describe the measures you can take against electrostatic build-up. We will look at the following points in more detail:
- What is ESD?
- ESD vs. anti-static
- Preventing electrostatic build-up and anti-static
- ESD clothing
- Anti-static clothing
- Earthing using ESD work shoes
Electrostatic discharge – what is ESD?
ESD stands for “electrostatic discharge”. Unlike anti-static, electrostatic discharge is not dangerous for people themselves, but is dangerous for very sensitive electronic components. People can generate dangerous voltages through friction, electrostatic induction or contact build-up. If the voltage exceeds just 100 volts, it can seriously damage electronic components. The problem is that people only notice this kind of power surge from approx. 3,500 volts. In this instance therefore, the victim is not the employee who causes the uncontrolled discharge, it’s the one who, in case of doubt, is responsible for an incorrectly functioning end device.
ESD vs. anti-static – what’s the difference?
In this context, anti-static properties are safety-relevant properties of a safety shoe or work shoe and offers employees protection against hazards caused by the ignition of flammable substances or fumes, or limited protection against electric shocks up to 250 volts, for example. An electrical charge is friction that a person generates through movement – e.g. by rubbing their upper arms on the sides of their torso when walking. If this dangerous energy is then suddenly released, an air-dust or air-gas mixture can ignite and cause an explosion. The victim in this case would be the employee themselves.
The area of application of the two static charges also differs:
- Electrostatic discharge (ESD) occurs during work on and with sensitive components in the semiconductor, electronics, automotive and pharmaceutical industries.
- Anti-static on the other hand occurs in potentially explosive environments in the chemical industry, fuel depots, refineries, silos, and in conveying, mixing and milling plants.
Preventing electrostatic build-up and anti-static
There are several measures you can take to protect yourself from electrostatic build-up and anti-static:
Two further factors encourage electrostatic build-up and discharge: humidity and temperature. For example, a dry environment with a humidity of approx. 20% causes much higher charges when two materials come into contact than the same process at 65% humidity. The risk of static build-up is therefore much lower in summer than in winter. However, excessive humidity in the ESD area has an unfavourable effect on soldering behaviour and accelerates corrosion.
Alongside the environmental factors, we’ll now take a closer look at the above-mentioned measures against electrostatic build-up and anti-static.
ESD clothing
Since electrostatic discharge does not pose a danger to people, but instead damages objects, PPE is not used in ESD areas. Nevertheless, ESD clothing must comply with a specific standard: the ESD standard IEC 61340-5-1. Even if it is not part of the personal protective equipment, the clothing must meet high standards: the low voltage range (from 100 volts upwards) in which the clothing must prevent electrostatic build-up or dissipate it in a controlled manner demands complex material requirements.
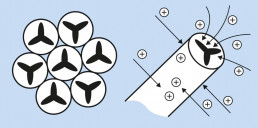
In the past, clothing made of 100 per cent cotton was usually used in ESD areas. Like all natural fibres, its advantage is that it builds up only a small amount of anti-static charge, even without additional finishes. However, humidity plays an important role here: the natural material is inherently hygroscopic – i.e. it absorbs moisture from the air – which improves its discharge capacity in a highly humid environment. However, if the air is drier, the cotton garment no longer retains the moisture in its fibres – it loses its natural discharge capacity and can become dangerously charged. Cotton also runs the risk of shedding its staple fibres. Due to different charges, these fibres then stick to the components and also lead to problems. These can be prevented by using long, high-quality staple fibres.
On the other hand, synthetic fibres such as polyester are continuous fibres, which greatly reduces the contamination caused by loose fibres. Unlike cotton, however, these are not hygroscopic, which is why the fibres become highly charged through friction. To limit this build-up and to comply with both the anti-static and ESD standards, additional fibres or yarns, like the conductive Resistat® and the dissipative Nega-Stat®, must be added to the garment. Resistat® has a synthetic core with a carbon coating, while Nega-Stat® has a carbon core with polyester coating. Adding these fibres/yarns has now become standard practice, a practice which is also used for mixed fabrics and 100% cotton fabrics.
The use of carbon minimises resistance and supports the controlled dissipation of the charge. Due to specified test procedures, the dissipative/conductive fibres must always be on the outside in an ESD area. In addition, the yarn on woven fabrics must always be woven in a mesh pattern (maximum distance of 5 x 5 mm2 per square) to enable the required dissipation of the charge. With weft- and warp-knitted fabrics, the yarn must be integrated into the machine weave due to the design. Dissipative/conductive yarn is also used for the joining seams.
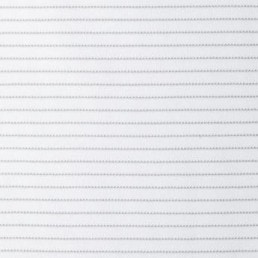
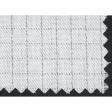
Anti-static clothing
Because anti-static clothing protects people directly, it is categorised as personal protective equipment (PPE) and must comply with standards EN 1149-5, EN ISO 13688 and 2016/425. While in ESD areas covering the upper body is sufficient, anti-static clothing must always consist of a combination of jacket and overalls or trousers. The material is made of a basic fabric that has been finished with special fibres or yarns to increase its discharge capacity. Synthetic fibres with hygroscopic properties are also used. For anti-static purposes, it does not matter whether the core or the coating is dissipative or conductive. However, here too, a mesh (smaller than 10 x 10 mm2) or yarns arranged in parallel (at a distance of less than 10 cm) must be integrated on the surface in order to comply with anti-static standard EN 1149-3.
Earthing and dissipation through ESD work shoes
The basic requirement for the unrestricted function of the clothing, independent of the standard, is the earthing of the wearer. This is done in the working environment that requires the anti-static protection, often in the form of a suitable footwear-floor system. This earthing system is usually also used for stationary and mobile activities in an ESD environment. Seated activities, on the other hand, (additionally) require a wrist strap to enable potential equalisation despite minimal contact with the floor.
A distinction is made between the anti-static properties and the ESD capacity of work shoes. It’s often asked whether ESD clothing can also be used in anti-static areas and vice versa. Unfortunately, a comparison with regard to the antistatic properties of ESD clothing and antistatic clothing is not as clear cut as it is with safety shoes. For shoes, the resistance specified in the standard applies, whereby the values can be compared with each other in an easily understandable way.
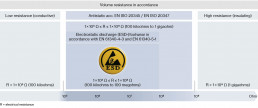
A safety shoe is anti-static if the resistance is between 100 kiloohms (105 ohms) and 1 gigaohm (109 ohms). According to the standard, a lower contact resistance means it is considered conductive, a higher contact resistance, insulating. As ESD work shoes are intended to protect electronic components against electrostatic build-up, the limit of the resistance here is 100 kiloohms and the upper limit 100 megaohms (1 x 108 ohms) – this means that ESD shoes are also always anti-static. These are given the ESD marking. However, anti-static work shoes are not always simultaneously ESD-capable: if a contact resistance of more than 100 megaohms is measured, the shoe is anti-static, but outside the ESD limits and therefore not ESD-capable. Instead of an ESD marking, these receive a safety or occupational shoe marking, e.g. A or S1 to S5 or O1 to O5.
ESD-certified safety shoes from uvex are available in many variants and with a wide range of features for multiple applications. Your sales representative will be happy to help you identify and select models suitable for your area of work.
An “electrifying” topic in the truest sense of the word, and one which we hope we have demystified for you in this article. If you have any further questions, please do not hesitate to contact us and we will advise you on the appropriate product selection for your area of work.