The ancient city of Babylon once lay in what is now Iraq, about 90 kilometres south of Baghdad. The erstwhile commercial metropolis is considered the birthplace of operational safety, with documents on this issue written in cuneiform as far back as 2000 BC. But a lot has happened since then. Come with us on a journey through the different ages of operational safety – from Mesopotamia and Ancient Rome to the 21st century.
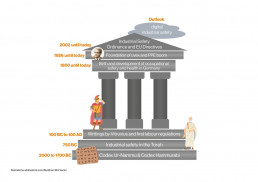
We begin our tour with the Code of Hammurabi, a legal text written in cuneiform, composed in around 1700 BC and named after the eponymous sixth king of the First Dynasty of Babylon. Of the 282 laws carved onto the stone stele, 40 deal with operational safety and define principles that are still valid today. The two most important:
- Companies (then: merchants) are responsible for the safety of their employees and liable for dangerous working conditions. (Law 6)
- Workers who cause an accident can be held accountable. (Law 117)
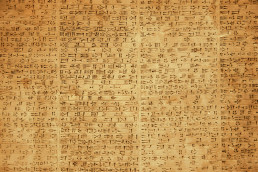
Did you know?…Cuneiform was the preferred writing system in the Middle East until around 1000 AD and was used to write several languages. It is characterised by horizontal, vertical and diagonal wedge-shaped impressions, which were usually made with a reed or wooden stylus on tablets of wet clay. The oldest surviving legal text of this kind is the Ancient Babylonian Code of Ur-Nammu, which was created in around 2000 BC on the orders of King Ur-Nammu of Ur in Mesopotamia. This document also contains very early, albeit still very abstract, statements on operational safety.
It wasn’t only in Babylon that operational safety was already a topic of discussion. The topic also appeared in 750 BC in various contexts in the Five Books of Moses, the Jewish Torah. For example, Exodus, Chapters 22:4 and 22:5 deal with compensation for field fires caused by negligence. Operational safety is dealt with implicitly here but in a way that is still far removed from our present-day understanding of the concept.
In Ancient Rome, operational safety precautions first appeared in around 20 BC in the writings of Roman architect Marcus Vitruvius Pollio (or ‘Vitruvius’ for short). In his work ‘De architectura’, Vitruvius describes some of the safety measures used in Rome’s large thermal baths to prevent accidents. These include a ban on flammable materials in the baths and an adherence to strict cleaning protocols. Usually however, there were significant gaps in occupational health and safety in the Ancient Roman workplaces of the time.
Firstly, the necessary safety precautions to protect workers against accidents were often lacking. And secondly, dangerous or unhealthy working conditions were often simply accepted. This resulted in many workers being injured or even killed. In order to resolve these problems, tradespeople in Ancient Rome were supposed to inspect their workplaces and take the necessary safety precautions themselves. Accordingly, the magistrates – as representatives of the Roman city government were then called – laid down specific guidelines for businesses that were intended to provide a safe and healthy working environment for their employees. For example, these included:
- an upper limit to the daily working time
- the scheduling of rest periods for employees
- the provision of appropriate equipment and accommodation
and
- a work ban for some trades in excessively poor weather conditions.
In Ancient Rome therefore, there was already a whole series of laws and regulations that governed operational safety and occupational health and safety. These were aimed primarily at minimising the risk of accidents. However, in many cases, workers in Ancient Rome were left to their own devices and ultimately had to decide for themselves whether they would take risks at work or not – but usually had no other choice.
Definitions: are operational safety and occupational health and safety the same thing?
In short: no. Operational safety and occupational health and safety are two very different concepts. Operational safety has a number of meanings and can be important both for companies and for employees. Today, operational safety refers to the safety of a company’s systems, equipment and processes. This includes possible sources of danger for employees, customers or even the environment.
On the other hand, occupational health and safety includes all concrete measures intended to guarantee the safety of employees at the workplace, for example, wearing protective equipment, compliance with safety regulations and awareness of potential hazards in the job. Operational safety is therefore another term for prevention, while occupational health and safety is aimed mainly at the derivation and implementation of concrete protective measures for employees.
Development of occupational health and safety in Germany
Let’s jump from the ancient forerunners of operational safety straight into the century before last. Occupational health and safety in Germany has its roots in the early 19th century. It was then that the first German laws and directives on the protection of employees against dangerous or unhealthy working conditions were passed. The reason for this was the advent of industrialisation, which brought with it mechanisation in the factories and thus new safety risks. Further operational safety measures, such as the introduction of the factory inspectorate (1891) and of employers’ liability insurance associations (from 1885), were required.

In the Germany of the 19th century, there was effectively no uniform occupational health and safety law. Instead, working conditions were regulated by the companies themselves. However, this often resulted in very poor working conditions. That’s also why in 1883 a law on health insurance and in 1884 a law on accident insurance for workers were passed in the German parliament. This represented a huge step in the history of German occupational health and safety.
However, it wasn’t until 1974 that the Occupational Safety Act obliged companies over a certain size to employ a company medical officer, for example. In 1996, the comprehensive German Occupational Health and Safety Act finally became a reality – after many decades of rollouts, upheavals, derogations and reforms. Since then, the Occupational Health and Safety Act has been extended to include various amendments. However, the central aim of the Act was and is operational risk assessment.
In our blog article on the ‘risk matrix according to Nohl’, read more on this topic and find out how you can systematically and objectively assess risk in your own company.
uvex does pioneering work in the field of operational safety
The year 1926 was also a ground-breaking one for occupational health and safety in Germany. In the Poppenreuth district of Fürth, export merchant Philipp M. Winter founded uvex’s predecessor company ‘Optische-Industrie-Anstalt Philipp M. Winter’. The development of the first safety eyewear, which was intended to protect against metal splinters or sparks when drilling, machining or welding, saw the introduction of ground-breaking PPE products during the 1930s. In 1964, the founder’s son Rainer Winter then developed the’ uvex’ brand we still know today – a milestone.
Philipp M. Winter, born on 3 May 1898 in Furth im Wald, was a pupil at Fürth Secondary School. After the First World War, he began his career by working as an export merchant, focussing on Spain and Portugal.
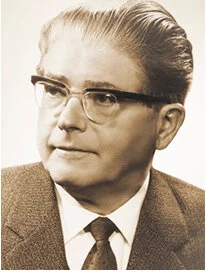
Operational safety in Germany – the current situation
Today, operational safety rules in Germany are still laid down in the Ordinance on Industrial Safety and Health. However, a new EU-wide operational safety directive is planned, which means that the existing Ordinance on Industrial Safety and Health as well as the Technical Regulations for Operational Safety will soon be replaced. The corresponding EU directive will still need to be implemented in national law, however. The aim is to further improve occupational safety in the EU and to substantially reduce the rate of accidents.
To ensure this, the requirements for operational safety have once again been significantly increased. For example, in accordance with the initial drafts of the directive by the European Commission, companies will in future be obliged to adopt a safety management system (SMS) and to have it reviewed regularly. In doing so, the companies will also have to rely on their employees’ cooperation. However, the adopting of an SMS is not yet mandatory, but merely a recommendation of the EU Commission until the directive is transposed into national law.
Did you know?…In 2021, the number of reportable workplace accidents in Germany according to a study by the German Statutory Accident Insurance (DGUV) was at around 759,993. Although this was 45,514 more than the previous year, it was still significantly fewer than 2019 (811,722). This can also be attributed to the increasing number of employees who have been working from home since the start of the COVID-19 pandemic.
Outlook: operational safety and the PPE of the future
In addition to all the legal amendments, the operational safety of the future here in Germany should continue to improve thanks to digitalisation as well as increasing connectivity. For example, data from different systems can be merged and analysed to detect and eliminate job hazards at an early stage. Automation is also playing an increasingly important role in making processes safer and more efficient.
In particular, personal protective equipment (PPE) is becoming lighter, more comfortable and more effective thanks to new technologies and more advanced materials. For example, future helmet designs will probably offer better absorption of impact energy as well as an improved field of vision and increased respiration circulation. The new helmets can then also be equipped with state-of-the-art communication systems, so that employees can talk to each other and collaborate in real time.
The protective suits of tomorrow also promise improved performance. Built-in sensors that can detect hazards early and warn the person wearing the suit could become standard within the next few years. It will also be possible to connect PPE suits with other electronic devices to ensure optimal functionality. Incidentally, we also enable PPE to be equipped from head to toe with sensors and actuators with our uvex techware product range.
uvex already offers an extensive range of occupational health and safety equipment that meets individual requirements in terms of safety, comfort and protection. Our product portfolio includes head, ear, eye, respiratory and foot protection, as well as gloves and clothing. It covers various areas of application, so you always have the right equipment for your situation. Take a look at our official online shops for business customers or private customers and discover our entire range of PPE products.