Every job is different and yet they all have one thing in common: they are associated with many small and large risks, which can cause accidents or work-related illnesses. But how can the risk situation in your company be assessed systematically and objectively? With the risk matrix according to Nohl. Read on to find out how to use it.
Starting point: the interaction of hazard and risk
As a PPE officer or employer, you are constantly on the lookout for potential hazards to your employees. And where there are hazards, there are risks. In occupational safety and health, risks arise whenever employees can come into spatial or temporal contact with an “injury-causing factor”. These factors can lead to accidents and injuries. In a workplace context, examples may include hot surfaces, flying sparks, moving surfaces or even unsafe traffic routes.
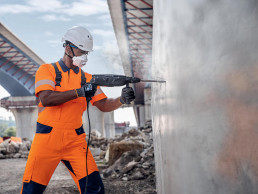
Risk assessment using basic formulas
In principle, the risk value of any work situation can be determined with the help of a relatively simple formula. Its origins lie in the insurance industry, and it is:
Risk value (RV) = probability of occurrence (PO) x severity of damage (S)
Theoretically, it is thus possible to easily add the risk values calculated for certain risk events (work situations) to find an overall value. The catch: by using this method, each individual risk is considered in isolation and specific influences on a workplace are not taken into account. The significance of the overall value is therefore severely limited.
Another occupational health and safety factor was therefore added to this formula. The probability of occurrence (PO) is also multiplied by the duration or frequency of a hazard (H), as follows:
Risk value (RV) = probability of occurrence (PO) x hazard duration/frequency (F) x severity of damage (S)
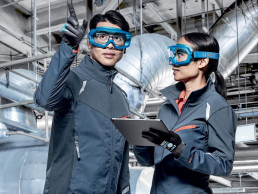
But even with this formula, it is not easy to provide meaningful values for factors such as “severity of damage (S)” based on operational data. However, since employers are obliged under §5 of the German Occupational Health and Safety Act (ArbSchG) to carry out a thorough assessment of potential hazards and safety risks in the workplace, the use of a system is essential. This is where the risk matrix according to Nohl comes into play.
So what exactly is a risk matrix?
The basis for a comprehensive occupational safety policy in the workplace is the risk assessment. A risk matrix is used to visualise operational risk situations and is the result of risk analysis and risk assessment. The risk matrix according to Nohl has established itself as an important and frequently used instrument in the field of occupational health and safety.
With its help, risks can be assessed depending on the company and job context and appropriate occupational health and safety measures can be introduced. For this purpose, the individual hazards are assigned to one of usually three – depending on the model, even up to five – risk levels, taking into account their probability of occurrence and potential severity of damage.
Important: To classify the hazards, you can either use statistics or estimate the risks based on experience and common sense. It is also possible to include specific characteristics of individual people (age, height, disabilities) in the risk assessment.
How does the risk matrix according to Nohl work?
The risk matrix is usually presented in tabular form. The severity of damage is noted (ascending) on the x-axis, the probability of occurrence (ascending) on the y-axis. The maximum risk results from the combination of a very high probability of occurrence and a very high (potential) extent of damage.
The following levels are initially used to classify the probability of occurrence (y-axis):
- Very low
- Low
- Medium
- High
The severity of damage (x-axis) is categorised in a similar way, as follows:
- Minor injuries or illnesses (e.g. minor cut, person can continue working)
- Moderately severe injuries or illnesses (e.g. simple bone fracture, person probably requires time off work)
- Severe injuries or illnesses (e.g. paraplegia, irreparable permanent damage is possible)
- Possible death or disaster (e.g. severe injuries to many people, long-term damage)
After identifying and defining both areas, you get a measured value, also called a risk indicator. This is usually between 1 and 7. It is intended to help determine whether and to what extent risk reduction measures should be taken. Risks are commonly classified as follows:
- Risk indicators 1-2: low risk, no risk reduction necessary (between residual risk and borderline risk, injuries very unlikely)
- Risk indicators 3-4: significant risk, risk reduction necessary (between close to and slightly above the borderline risk, damage likely)
- Risk indicators 5-7: high risk, risk reduction urgently necessary (above the borderline risk, injury very likely)
Now it is up to you what kind of colour coding system (e.g. traffic light colours) you use to classify the risk indicators of your matrix. For example, you can further differentiate your traffic light colours by adding different shades of green, yellow or red.
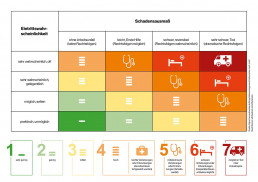
A risk matrix according to Nohl may look something like this. It is important that colour coding similar to a traffic light system shows how dangerous a possible incident can become, as it can be used to identify critical areas and derive suitable measures.
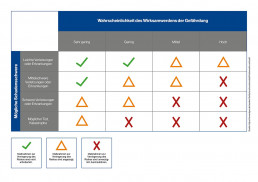
Risk matrices can be presented in many different ways. For example, severity of damage and probability of occurrence are sometimes shown on the x-axis, sometimes on the y-axis. It is important that critical hazard areas can be identified at a glance.
Creating your own risk matrix: what you need to do
First things first: there is no standard procedure for risk assessment. You alone decide the details of how you want to proceed. Nevertheless, seven main process steps have become established in practice:
- Identify operational structure & prepare analysis:
First, divide your company into manageable areas. Differentiate between workplaces and activities. In the same step, compile relevant occupational health and safety regulations and sector-specific rules.
- Identify hazards & name sources:
When doing this, take into account safety-related relationships between workplaces, tasks, work equipment, processes or procedures and record all hazards as well as physical and psychological stresses on site.
- Assess hazards & identify risks:
In the next step, assess whether existing measures are sufficient or whether new occupational safety and health measures are required. Use the risk matrix according to Nohl to estimate the probability of occurrence and the extent (severity) of the hazards. The risk indicator determined (see section above) helps shape further action planning strategies.
- Define protection goals & determine measures:
Now eliminate (as far as possible) potential sources of danger, e.g. by replacing a dangerous substance or process with a less dangerous alternative. Define technical, organisational and personal protection measures and objectives. At the same time, you should also ensure that your employees are adequately trained (qualified).
- Implement measures & define organisational framework:
Once all this is done, implement the measures effectively. In doing so, check whether measures have been fully implemented and hazards therefore minimised. For all measures, define concrete responsibilities, (review) dates and communication procedures or operating instructions. This helps you create transparency in the long term.
- Check effectiveness & readjust measures
The long-term success of risk prevention depends on the effectiveness of your measures. Critically check whether technical measures are effective, employees are disregarding defined measures or existing protective devices can be tampered with. If necessary, fine-tune your safety policy at critical points.
- Document results & repeat assessment
Going forward, continuously document the results of your risk assessment as well as derived measures and review results. In doing so, continue adapting the risk assessment and update it regularly (about every two years). This ensures you always stay up to date with changes to regulations, new technological advancements and any other developments.
CONCLUSION: You have seen that a risk assessment should not be seen as a one-off process. Instead, it involves recurring processes aimed at constantly improving occupational health and safety. Many other work steps, including the determination of appropriate measures and their continuous monitoring for effectiveness, build on a risk matrix such as the one according to Nohl.
Have you created your own risk matrix according to Nohl and are now wondering which uvex safety products are suitable for the specific hazards in your workplace? Contact our Service team, who will be happy to advise you.