In many jobs, employees face particular health and safety hazards. In these jobs, the right to life and physical integrity (German Basic Law, § 2), which also applies in the workplace, is applicable. Therefore, in 1996, the legislator stipulated in the German Occupational Health and Safety Act (ArbSchG) how “the safety and health of employees at work are to be ensured and improved through occupational health and safety measures” as well as who is responsible for their implementation (§ 1 ArbSchG, Objectives and Scope). Occupational health and safety refers to all measures, methods and means aimed at protecting workers from hazards to safety and health in the workplace. Occupational health and safety can be divided into the subcategories of occupational safety and health protection.
What does occupational health and safety entail?
A distinction can be made between four types of occupational health and safety: general, technical, social and medical.
General occupational health and safety focuses on safe working conditions aimed at protecting the health and lives of employees. The employer is responsible for developing occupational health and safety measures and providing employee training on these measures. In turn, employees must comply with the measures, while also taking responsibility for their own health and safety.
Technical occupational health and safety refers to the health and safety of employees, including in relation to contact with hazardous substances, machinery, noise, radiation and vibration. It also refers to safety in the workplace or in the facility in general, for example through the provision of escape and rescue plans or regular inspections of the lifts.
Social occupational health and safety regulates the protection of children, young people and expectant or nursing mothers in the German Child Labour Act, Young Persons Employment Act and Maternity Protection Act. Regulations governing protection for disabled people and working time are also included here.
Finally, medical occupational health and safety consists of an inspection process in which experts – such as medical officers – inspect the workplace for work-related illness, accident and hazard risks. In addition, medical occupational safety includes having first aiders available for emergencies and reporting suspected work-related illnesses or accidents to the accident insurance organisation. In addition to this technical distinction, occupational health and safety can also be divided into the subcategories of occupational safety and health protection in terms of content:
Occupational safety – avoiding safety hazards and risks at work
The aim of occupational safety is to enable a hazard-free working environment for employees and to reduce and control potential hazards in order to achieve this. Hazards can be caused by the improper use of machines, work processes, work materials, by “physical, chemical and biological influences” and by psychological stress at work (§ 5, para. 3 ArbSchG), for example. According to Paragraph 4 of the German Occupational Health and Safety Act, hazards arise as a result of the meaningful combination of “technology, work organisation, other working conditions, social relationships and the influence of the environment on the workplace”. This is because safety hazards can sometimes only be recognised from the interaction of the individual factors.
This is what the risk assessment mentioned in Paragraph 5 refers to: potential hazards and risks must be identified, and appropriate protective measures taken to avoid them. Risk assessment is a process aimed at continuously improving working conditions and health protection. The BGW (Employer’s Liability Insurance Association for Health Services and Welfare Care) provides instructions for the seven-step risk assessment.
Health protection – preventing health problems and work-related illnesses
The aim of health protection is to protect employees from long-term, work-related damage to health and illnesses, and to prevent these as far as possible. Health protection includes all measures aimed at preventing damage to health. Illnesses can be caused by physical, chemical, psychological and biological factors. According to Paragraph 4 of the German Occupational Health and Safety Act, this refers to both physical and mental health. Health protection also includes occupational medicine as effective preventive healthcare at work. This involves preventive medical check-ups, suitability assessments for certain activities, employee information, first aid, support for employees with reduced ability etc.
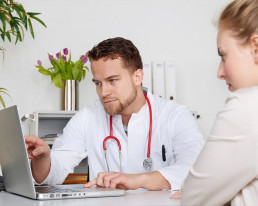
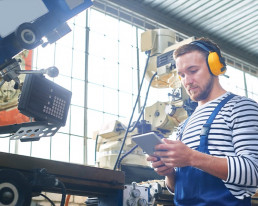
What practical occupational safety measures can be taken?
Occupational health and safety measures should protect people from the source of danger and keep them at a safe distance from it. This can be implemented using technical, organisational or personnel-related measures:
- Technical occupational safety measures are intended to separate people spatially from the source of danger and to avoid or eliminate existing or potential hazards before they arise. Examples here include equipment safety, separating protective devices to protect employees from a hazardous area by means of a physical barrier (such as fencing, protectors etc.), implementation of ergonomic design requirements relating to health protection and protection against physical reactions.
- Organisational occupational safety measures separate people spatially and temporally from the source of danger. These are most evident in the organisation, work processes, information, tasks, working time management and restrictions or prohibitions in relation to work.
- Personal health and safety measures refer to employees’ personal protective equipment and their behaviour. They involve applying recognised safety measures and complying with regulations. However, they also include the passing on of information to employees in the form of briefings, instructions, training, operating instructions etc.
These occupational health and safety measures are listed here in order of priority – after the prevention or elimination of the source of danger, the focus is on technical, then organisational and finally personal protective measures. The occupational health and safety measures that affect a group have priority over those that affect individuals.
You can find useful information on how occupational safety measures can be implemented on construction sites and the sources of danger found there in the uvex x-pertblog.
Who is responsible for occupational health and safety in the workplace?
To ensure that occupational health and safety does not remain merely theoretical, officers dedicated to the issue and who translate occupational health and safety theory into practical regulations are required. According to the legislator, both employers and employees are responsible for implementing the German Occupational Health and Safety Act:
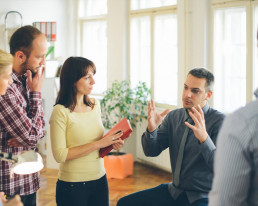
According to Paragraph 5, the task of the employer is to identify the hazards to employees in the workplace (risk assessment) and to determine necessary occupational health and safety measures. The different activities should be assessed individually, unless the nature of the working conditions is the same. Subsequently, necessary measures should be decided upon, “taking into account the circumstances”, their effectiveness reviewed and, if necessary, adapted to changed conditions (§3 ArbSchG, para. 1). Safety experts, safety officers and the occupational health and safety committee can be appointed to carry out these tasks. In some companies, the manager is also responsible for assessing occupational health and safety. The latter then seeks support for the professional assessment of workplace hazards, if necessary.
In addition, the manager must ensure that the “appropriate organisational structures” and “necessary resources” are in place to implement the measures. They are also responsible for publicising the decisions within the workplace and ensuring that they are taken into account in the “operational management structures” (§ 3 ArbSchG, para. 2). The costs for this cannot be passed on to the employees but must be borne by the company (para. 3).
Important aspects of the German Occupational Health and Safety Act are also explained in the x-pertblog article “Organising occupational health and safety in the company”.
Responsibility of the employees
Employees are informed of and trained in the necessary and appropriate occupational health and safety measures. According to Paragraph 15 of the German Occupational Health and Safety Act, they are obliged to ensure their health and safety at work. They are obliged to comply with and follow their employer’s instructions. They must also be mindful of the health and safety of the people their work impacts. Above all, it is important to “use machines, equipment, tools, work materials, means of transport and other work equipment as well as protective devices and the personal protective equipment provided for their intended purpose” (§ 15 ArbSchG). In addition, employees must immediately report any hazards or defects in protective systems to their supervisor, the occupational safety specialist, the medical officer or the safety officer (§ 16 ArbSchG).
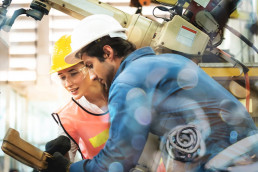
Implementation of occupational health and safety measures
Written operating instructions are a suitable method of publicising the occupational safety measures within the company (see § 9 of the German Ordinance on Industrial Health and Safety). They are the basis for occupational health and safety instructions and explain in comprehensible form and language the desired behaviour in the workplace and when performing tasks. There is one set of operating instructions per activity. Depending on the degree of danger and the field of work, employee training is crucial in ensuring that all employees know about the potential danger and how to work safely with machines, substances and processes. It is then the task of the manager with authority to issue instructions to ensure that the occupational health and safety measures are implemented and, if necessary, to enforce them. Well-planned occupational health and safety measures will also pay off at the next occupational health and safety inspection by the state authorities.
Who checks the implementation of occupational health and safety in workplaces?
Compliance with the German Occupational Health and Safety Act is monitored by the competent state offices for occupational health and safety or the labour inspectorates, which can also advise the employer on their obligations (§ 21, para. 1 ArbSchG). The employer or an officer is obliged to provide the official with all necessary information and documents. In order to be properly prepared for this, the risk assessment and the occupational health and safety measures used in the company must be documented. In addition, employers are obliged to appoint responsible contact persons (occupational safety specialists, medical officers, safety engineers and safety officers) in advance, which is regulated in the Occupational Safety Act alongside employers’ other safety-related duties.
The official also has the right to inspect all premises and rooms, to check everything and to prescribe occupational health and safety measures. Furthermore, the statutory accident insurance institutions (DGUV), the industrial trade associations also check compliance with the statutory regulations.
Anyone – including employees – who contravenes the legal occupational health and safety regulations will be fined up to EUR 5,000. Any employer or officer who violates the enforceable regulations of the authority may be fined up to EUR 25,000 (§ 25 Provisions Regarding Fines ArbSchG). Anyone who persistently and repeatedly violates these official regulations or “endangers the life or health of an employee through a deliberate act” will receive a custodial sentence of up to one year or a fine (§ 26 Criminal Provisions ArbSchG).
uvex as a partner for comprehensive occupational safety
Once you realise the importance of occupational health and safety for your employees, you will want to know how to put the theory into practice. uvex provides your employees with high-quality personal protective equipment to help you do this. Our comprehensive range includes safety helmets, safety glasses, hearing protection, respirators, protective clothing and workwear, safety gloves and safety shoes. In addition, uvex also produces customised protective equipment, including prescription safety spectacles, otoplastic hearing protection and medicare safety shoes that are individually adapted to the wearer’s foot.